Mastering The Calibration Of Temperature Measuring Devices: A Comprehensive Guide
For instance, in the medical field, a thermometer that isn’t calibrated correctly could misdiagnose a patient, while in manufacturing, it could result in defective products. Calibration bridges the gap between theoretical accuracy and real-world performance by aligning the device’s readings with a known standard. This process is not just a regulatory requirement in many sectors but also a best practice for maintaining operational efficiency. The significance of calibration extends beyond mere compliance. It ensures consistency in measurements, which is vital for maintaining quality control and adhering to industry standards. Over time, temperature measuring devices can drift from their original accuracy due to wear and tear, environmental factors, or manufacturing imperfections. Regular calibration helps detect and correct these deviations, ensuring that the device performs as expected. By investing in calibration, businesses not only safeguard their operations but also enhance their reputation for reliability and precision. This article will delve into the nuances of calibration, exploring its importance, methods, and best practices while addressing common questions and challenges. As we navigate through the complexities of calibration, it’s essential to understand that this process is not a one-size-fits-all solution. Different industries and applications demand specific calibration techniques and frequencies. For example, a laboratory thermometer might require more frequent calibration than an industrial sensor used in less critical applications. This article will guide you through the steps of calibrating temperature measuring devices, highlight the tools and standards used, and provide actionable insights to help you optimize your calibration processes. Whether you’re new to the concept or looking to refine your existing practices, this guide will equip you with the knowledge to master the art of calibration.
Table of Contents
- Why Is Calibration of Temperature Measuring Devices Important?
- How Often Should Temperature Measuring Devices Be Calibrated?
- What Are the Methods of Calibration for Temperature Measuring Devices?
- Tools and Standards Used in Calibration
- Step-by-Step Guide to Calibrating Temperature Measuring Devices
- What Are the Common Challenges in Calibration?
- Best Practices for Effective Calibration
- How Does Calibration Impact Different Industries?
Why Is Calibration of Temperature Measuring Devices Important?
Calibration of temperature measuring devices is a cornerstone of accuracy and reliability in countless applications. In industries such as pharmaceuticals, aerospace, and food processing, even the slightest deviation in temperature readings can have significant consequences. For example, in pharmaceutical manufacturing, precise temperature control is essential for ensuring the efficacy and safety of medications. A thermometer that reads 2°C higher than the actual temperature could lead to improper storage conditions, rendering the product ineffective or unsafe for use. Similarly, in aerospace engineering, temperature sensors are used to monitor critical components. An uncalibrated sensor might fail to detect overheating, potentially leading to catastrophic failures.
Beyond safety and compliance, calibration also plays a vital role in maintaining operational efficiency. In manufacturing, precise temperature control is often linked to energy consumption. Devices that are not calibrated correctly may cause machinery to operate inefficiently, leading to increased energy costs and reduced productivity. For instance, an industrial oven that runs hotter than intended due to an uncalibrated temperature sensor will consume more energy and may produce inconsistent results. Regular calibration ensures that devices operate within their specified tolerances, optimizing performance and reducing waste.
Read also:Understanding Steve Dulcichs Illness A Comprehensive Guide
Moreover, calibration fosters trust and credibility. Customers and regulatory bodies expect businesses to adhere to stringent quality standards. Regular calibration demonstrates a commitment to accuracy and accountability, enhancing a company’s reputation. For example, food processing companies that calibrate their thermometers regularly can assure customers that their products are safe for consumption. This trust is invaluable in competitive markets, where consumers are increasingly aware of quality and safety standards. By prioritizing calibration, businesses not only protect their operations but also build a foundation of reliability and excellence.
How Often Should Temperature Measuring Devices Be Calibrated?
The frequency of calibration for temperature measuring devices depends on several factors, including the type of device, its application, and the environment in which it operates. For critical applications, such as medical diagnostics or pharmaceutical production, calibration may be required as frequently as every three to six months. These industries demand the highest level of accuracy, and even minor deviations can have serious consequences. On the other hand, devices used in less critical applications, such as home appliances or general industrial processes, may only need calibration annually or biennially.
Environmental factors also play a significant role in determining calibration frequency. Devices exposed to harsh conditions, such as extreme temperatures, humidity, or vibrations, are more likely to drift from their calibrated state. For example, a temperature sensor used in an outdoor weather station may require more frequent calibration than one used in a controlled laboratory environment. Similarly, devices that experience heavy usage or are subject to frequent handling may also need more regular calibration to maintain accuracy.
Regulatory requirements and manufacturer recommendations are additional considerations. Many industries are governed by standards that mandate specific calibration intervals. For instance, ISO standards often require calibration at defined intervals to maintain compliance. Additionally, manufacturers typically provide guidelines on how often their devices should be calibrated. Ignoring these recommendations can lead to non-compliance and potential legal issues. By adhering to a well-planned calibration schedule tailored to the specific needs of the device and its application, businesses can ensure consistent performance and avoid costly errors.
What Are the Methods of Calibration for Temperature Measuring Devices?
Calibration of temperature measuring devices can be performed using various methods, each suited to specific applications and requirements. The two primary approaches are comparison calibration and fixed-point calibration. Comparison calibration involves comparing the readings of the device under test (DUT) with a reference standard that is known to be highly accurate. This method is widely used due to its simplicity and cost-effectiveness. For example, a laboratory thermometer can be calibrated by immersing it in a controlled water bath alongside a certified reference thermometer. The readings are then compared, and adjustments are made to the DUT if necessary.
Fixed-point calibration, on the other hand, relies on physical phenomena that occur at specific temperatures, such as the freezing or boiling points of pure substances. This method is more precise but also more complex and expensive. It is typically used for high-accuracy applications, such as calibrating thermometers for scientific research. For instance, the triple point of water, which occurs at 0.01°C, is a commonly used fixed point for calibrating thermometers. This method ensures traceability to international standards, making it ideal for applications where absolute accuracy is paramount.
Read also:Scarlett Johansson Height And Weight A Comprehensive Guide To Her Life And Career
Another emerging method is in-situ calibration, which involves calibrating the device in its actual operating environment. This approach is particularly useful for devices that are difficult to remove or transport, such as those used in industrial processes. In-situ calibration minimizes downtime and ensures that the device performs accurately under real-world conditions. However, it requires specialized equipment and expertise, making it less accessible for smaller operations. By understanding the strengths and limitations of each method, businesses can choose the most appropriate calibration technique for their needs.
Tools and Standards Used in Calibration
Calibration of temperature measuring devices relies heavily on specialized tools and adherence to internationally recognized standards. One of the most critical tools is the reference thermometer, which serves as the benchmark for accuracy during the calibration process. These thermometers are often certified by national metrology institutes and are designed to maintain their precision over time. For example, platinum resistance thermometers (PRTs) are widely used as reference standards due to their exceptional accuracy and stability. They are particularly effective in laboratory settings where precision is non-negotiable.
In addition to reference thermometers, calibration baths and dry-block calibrators are essential tools for creating controlled temperature environments. Calibration baths use liquids like water or oil to provide a stable temperature for testing, while dry-block calibrators use metal blocks with precise temperature control. These tools are indispensable for ensuring that the device under test (DUT) is exposed to uniform and accurate temperature conditions. For instance, a calibration bath might be used to test a batch of thermometers at a specific temperature range, ensuring consistency across multiple devices.
Adherence to standards is equally important in the calibration process. Organizations such as the International Organization for Standardization (ISO) and the National Institute of Standards and Technology (NIST) provide guidelines that ensure traceability and reliability. For example, ISO 17025 is a globally recognized standard for testing and calibration laboratories, emphasizing the importance of quality management and technical competence. Similarly, NIST traceability ensures that calibration results can be linked to national standards, providing confidence in the accuracy of the measurements. By using the right tools and following established standards, calibration processes can achieve the highest levels of accuracy and reliability.
Step-by-Step Guide to Calibrating Temperature Measuring Devices
Calibrating temperature measuring devices is a meticulous process that requires attention to detail and adherence to best practices. The first step is to gather the necessary tools, including a reference thermometer, a calibration bath or dry-block calibrator, and any documentation required for recording results. Once the tools are ready, the next step is to prepare the device under test (DUT) by ensuring it is clean and free of any physical damage that could affect its performance. For example, a thermometer with a cracked bulb or a loose connection may yield inaccurate readings, making calibration ineffective.
The calibration process begins by setting the calibration bath or dry-block calibrator to the desired temperature. Once the temperature has stabilized, both the reference thermometer and the DUT are placed in the controlled environment. It’s crucial to allow sufficient time for the devices to reach thermal equilibrium before recording their readings. For instance, a thermometer immersed in a calibration bath should be left undisturbed for at least five minutes to ensure accurate results. The readings from the DUT are then compared to those of the reference thermometer, and any discrepancies are noted.
If the DUT’s readings deviate from the reference standard beyond acceptable limits, adjustments may be necessary. Many modern devices come with built-in calibration features that allow for easy adjustments. For example, digital thermometers often have a calibration mode that enables users to input correction factors. Once adjustments are made, the device should be tested again to confirm its accuracy. Finally, all calibration results should be documented, including the date, environmental conditions, and any adjustments made. This documentation not only serves as a record of compliance but also helps identify trends or recurring issues that may require further investigation.
What Are the Common Challenges in Calibration?
While calibration of temperature measuring devices is essential, it is not without its challenges. One of the most common issues is drift, which refers to the gradual deviation of a device’s readings from its calibrated state over time. Drift can be caused by factors such as wear and tear, environmental exposure, or manufacturing defects. For example, a thermocouple used in a high-temperature industrial furnace may experience drift due to oxidation or contamination of its sensing junction. Detecting and correcting drift requires regular calibration, but it can be difficult to predict when it will occur.
Another challenge is ensuring traceability, which is the ability to link calibration results to a recognized standard. Traceability is critical for maintaining accuracy and compliance, but it can be complicated by the use of outdated or uncertified reference standards. For instance, a laboratory using a reference thermometer that is not traceable to NIST standards may produce unreliable calibration results. To overcome this challenge, businesses must invest in certified reference standards and ensure that their calibration processes adhere to recognized guidelines, such as ISO 17025.
Finally, human error remains a significant obstacle in calibration. Mistakes in recording data, improper handling of devices, or incorrect adjustments can all compromise the accuracy of the process. For example, failing to allow sufficient time for thermal equilibrium during calibration can lead to inaccurate readings. To mitigate these risks, businesses should implement standardized procedures, provide adequate training for personnel, and use automated systems where possible. By addressing these common challenges, organizations can enhance the reliability and effectiveness of their calibration efforts.
Best Practices for Effective Calibration
To ensure the calibration of temperature measuring devices is both effective and efficient, it’s essential to follow a set of best practices. One of the most important practices is to establish a calibration schedule tailored to the specific needs of each device. This schedule should consider factors such as the device’s application, environmental conditions, and manufacturer recommendations. For example, a thermometer used in a hospital’s laboratory may require quarterly calibration, while one used in a home kitchen might only need annual calibration. A well-planned schedule helps prevent unnecessary downtime and
Exploring The Rhythmic World Of Step Music Genre: A Comprehensive Guide
Exploring The Advantages And Disadvantages Of Wave Power: A Comprehensive Guide
How Old Did Bilbo Live? Unveiling The Secrets Of A Hobbit's Lifespan
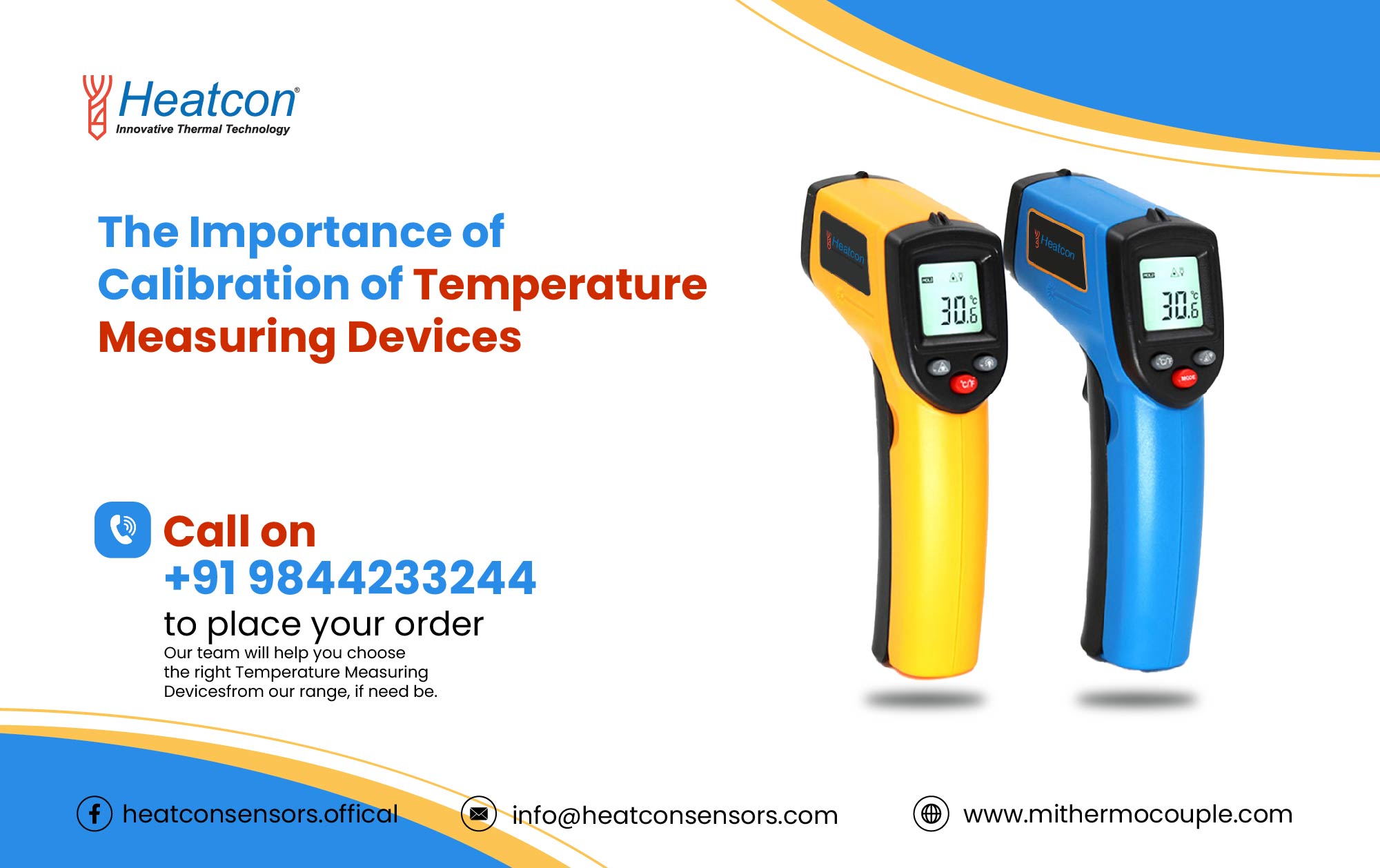
Importance of Calibration in Temperature Measuring Devices

Industrial Temperature Measuring and Monitoring Devices