What Is The Best Wire Size For 100 Amps? A Comprehensive Guide
Choosing the correct wire size for 100 amps is crucial for ensuring safety, efficiency, and compliance with electrical codes. Whether you’re setting up a new home electrical system, upgrading an existing one, or working on an industrial project, understanding the nuances of wire sizing can save you from costly mistakes and potential hazards. Wires that are too small can overheat, leading to fires, while oversized wires can unnecessarily increase costs and complicate installations. With so many factors to consider—such as wire material, insulation type, and environmental conditions—it’s essential to approach this topic with clarity and precision.
When it comes to handling 100 amps, electrical systems demand wires that can safely carry the current without excessive voltage drop or overheating. The National Electrical Code (NEC) provides guidelines that professionals rely on to determine the appropriate wire gauge, but these standards are often misunderstood or misapplied. Factors like the length of the wire run, ambient temperature, and whether the wire is enclosed or exposed further complicate the decision-making process. This guide will break down these considerations, ensuring you make informed choices.
In this article, we’ll explore everything you need to know about selecting the best wire size for 100 amps. From understanding the basics of electrical wiring to addressing common questions and concerns, we’ll cover the topic comprehensively. Whether you’re a DIY enthusiast or a seasoned electrician, this guide will equip you with the knowledge to confidently tackle your next electrical project. Let’s dive in!
Read also:Diane Furnberg Exploring Her Life Achievements And Impact
Table of Contents
- What Factors Affect the Choice of Wire Size for 100 Amps?
- How Does Wire Material Impact the Wire Size for 100 Amps?
- What Are the Best Practices for Wire Sizing in Different Environments?
- Why Is Voltage Drop Important When Selecting Wire Size for 100 Amps?
- How to Calculate the Right Wire Size for 100 Amps
- What Are the Common Mistakes to Avoid When Selecting Wire Size?
- Frequently Asked Questions About Wire Size for 100 Amps
- Conclusion
What Factors Affect the Choice of Wire Size for 100 Amps?
Selecting the right wire size for 100 amps involves considering several key factors that influence performance and safety. These factors include the wire material, insulation type, ambient temperature, and the length of the wire run. Each plays a critical role in determining the appropriate gauge for your electrical system.
Wire Material: Copper vs. Aluminum
Copper and aluminum are the two most common materials used for electrical wiring. Copper is highly conductive and more durable, making it the preferred choice for many applications. However, it is also more expensive. Aluminum, on the other hand, is lighter and less costly but requires larger gauges to handle the same current as copper. For example, a 1 AWG copper wire can carry 100 amps, while a 1/0 AWG aluminum wire is needed for the same load.
Insulation Type and Temperature Ratings
The type of insulation on the wire also affects its ampacity—the amount of current it can safely carry. Common insulation types include THHN, THWN, and XHHW, each with different temperature ratings. Wires with higher temperature ratings can handle more current without overheating. For instance, a THHN wire rated for 90°C can carry more amps than one rated for 75°C, even if they are the same gauge.
Ambient Temperature and Environmental Conditions
Environmental factors such as ambient temperature and exposure to moisture or sunlight can influence wire sizing. Higher ambient temperatures reduce the ampacity of wires, necessitating larger gauges. Similarly, wires installed in wet or damp locations require specific insulation types to prevent damage and ensure safety.
How Does Wire Material Impact the Wire Size for 100 Amps?
The choice between copper and aluminum wires is one of the most critical decisions when selecting wire size for 100 amps. Both materials have distinct advantages and disadvantages that directly affect their performance and suitability for various applications.
Advantages of Copper Wiring
Copper is renowned for its superior conductivity, corrosion resistance, and mechanical strength. These qualities make it ideal for applications where reliability and longevity are paramount. For 100-amp circuits, copper wires are typically smaller in diameter compared to aluminum wires, which simplifies installation and reduces the risk of overheating. For instance, a 1 AWG copper wire is sufficient for 100 amps, while aluminum would require a 1/0 AWG wire.
Read also:Jacob Lofland Net Worth Unveiling The Actors Career And Financial Journey
Advantages of Aluminum Wiring
Aluminum wiring is a cost-effective alternative to copper, especially for large-scale projects where budget constraints are a concern. While aluminum is less conductive than copper, it is lighter and easier to handle, making it suitable for long-distance runs. However, aluminum wires are more prone to oxidation and require special connectors to prevent loosening over time. This makes them less ideal for high-stress environments.
Cost vs. Performance: A Balancing Act
When deciding between copper and aluminum, it’s essential to weigh the upfront costs against long-term performance. Copper wires may have a higher initial cost, but their durability and efficiency often result in lower maintenance expenses. Aluminum, while cheaper, may require more frequent inspections and replacements, particularly in demanding conditions.
What Are the Best Practices for Wire Sizing in Different Environments?
The environment in which a wire is installed plays a significant role in determining the appropriate wire size for 100 amps. Different settings—such as residential, commercial, and industrial—present unique challenges that must be addressed to ensure safety and compliance.
Residential Applications
In residential settings, wires are often installed in walls, ceilings, or underground conduits. These environments typically require wires with moisture-resistant insulation, such as THWN or XHHW. For 100-amp service panels, a 2 AWG copper wire or 1/0 AWG aluminum wire is commonly used, depending on the distance from the main breaker panel.
Commercial and Industrial Settings
Commercial and industrial environments often involve higher ambient temperatures and exposure to chemicals or mechanical stress. In such cases, wires with higher temperature ratings and robust insulation are necessary. Additionally, longer wire runs may require larger gauges to minimize voltage drop and ensure consistent performance.
Outdoor and Underground Installations
For outdoor or underground installations, direct burial cables like UF-B are often used. These cables are designed to withstand moisture, UV exposure, and temperature fluctuations. Proper sizing is critical to prevent overheating, especially in buried conduits where heat dissipation is limited.
Why Is Voltage Drop Important When Selecting Wire Size for 100 Amps?
Voltage drop is a critical consideration when selecting the wire size for 100 amps, as it directly impacts the efficiency and performance of your electrical system. Voltage drop occurs when electrical current flows through a wire, causing a reduction in voltage along the length of the wire. Excessive voltage drop can lead to equipment malfunctions, reduced efficiency, and even safety hazards.
Understanding Voltage Drop Calculations
Voltage drop is calculated using the formula: Voltage Drop = (2 × Length × Current × Resistance) / 1000. The resistance of the wire depends on its material and gauge. For example, a 100-foot run of 2 AWG copper wire carrying 100 amps will have a lower voltage drop compared to a 1/0 AWG aluminum wire of the same length. To minimize voltage drop, larger wire gauges or shorter runs are often required.
NEC Guidelines for Acceptable Voltage Drop
The NEC recommends that voltage drop should not exceed 3% for branch circuits and 5% for feeder circuits. Adhering to these guidelines ensures that your electrical system operates efficiently and safely. For long wire runs, upgrading to a larger gauge can help maintain acceptable voltage levels and prevent performance issues.
How to Calculate the Right Wire Size for 100 Amps
Calculating the correct wire size for 100 amps involves a systematic approach that considers all relevant factors, including wire material, insulation type, and environmental conditions. By following a step-by-step process, you can ensure that your electrical system is both safe and efficient.
Step 1: Determine the Load Requirements
Start by identifying the total load your circuit will carry. For a 100-amp service, this typically includes major appliances, HVAC systems, and lighting. Ensure that the wire gauge you choose can handle the maximum expected load without exceeding its ampacity rating.
Step 2: Consult NEC Ampacity Tables
The NEC provides ampacity tables that specify the maximum current each wire gauge can carry under various conditions. For example, a 2 AWG copper wire is rated for 115 amps at 75°C, making it suitable for 100-amp applications. Always cross-reference these tables with your specific installation requirements.
Step 3: Account for Voltage Drop
Finally, calculate the voltage drop for your wire run and adjust the gauge if necessary. For long distances, upgrading to a larger wire size can help maintain optimal performance and prevent equipment damage.
What Are the Common Mistakes to Avoid When Selecting Wire Size?
Even experienced electricians can make mistakes when selecting wire size for 100 amps. Avoiding these common pitfalls can save you time, money, and potential safety hazards.
Mistake 1: Ignoring Environmental Factors
Failing to account for ambient temperature, moisture, or exposure to sunlight can result in undersized wires that overheat or degrade prematurely. Always choose wires with appropriate insulation for your specific environment.
Mistake 2: Overlooking Voltage Drop
Neglecting to calculate voltage drop can lead to inefficient systems and equipment malfunctions. Always factor in the length of the wire run and adjust the gauge accordingly.
Mistake 3: Using Incorrect Connectors
Using incompatible connectors, especially with aluminum wires, can cause loose connections and increase the risk of fire. Always use connectors specifically designed for the wire material you’re working with.
Frequently Asked Questions About Wire Size for 100 Amps
What is the minimum wire size for 100 amps?
The minimum wire size for 100 amps is typically 2 AWG copper or 1/0 AWG aluminum, depending on the length of the run and environmental conditions.
Can I use 1 AWG wire for 100 amps?
Yes, 1 AWG copper wire is suitable for 100 amps, provided it meets the insulation and temperature requirements for your application.
How do I know if my wire is oversized?
An oversized wire is not inherently dangerous but can increase costs and complicate installations. If your wire gauge significantly exceeds the NEC recommendations for your load and conditions, it may be oversized.
Conclusion
Selecting the correct wire size for 100 amps is a critical step in ensuring the safety, efficiency, and compliance of your electrical system. By considering factors such as wire material, insulation type, and environmental conditions, you can make informed decisions that meet your project’s needs. Remember to consult the NEC guidelines, account for voltage drop, and avoid common mistakes to achieve optimal results. Whether you’re a DIY enthusiast or a professional electrician, this guide provides the knowledge and tools to confidently tackle your next electrical project.
For further reading, check out this
Discover The Magic Of Vanillagift.comn: Your Ultimate Gift Solution
The Ultimate Guide To Understanding Seven Sided Regular Polygon: Geometry Simplified
Discover Unique Gifts At Vinillagift.com: Your Ultimate Gifting Destination

What Size Copper Wire For 40 Amps
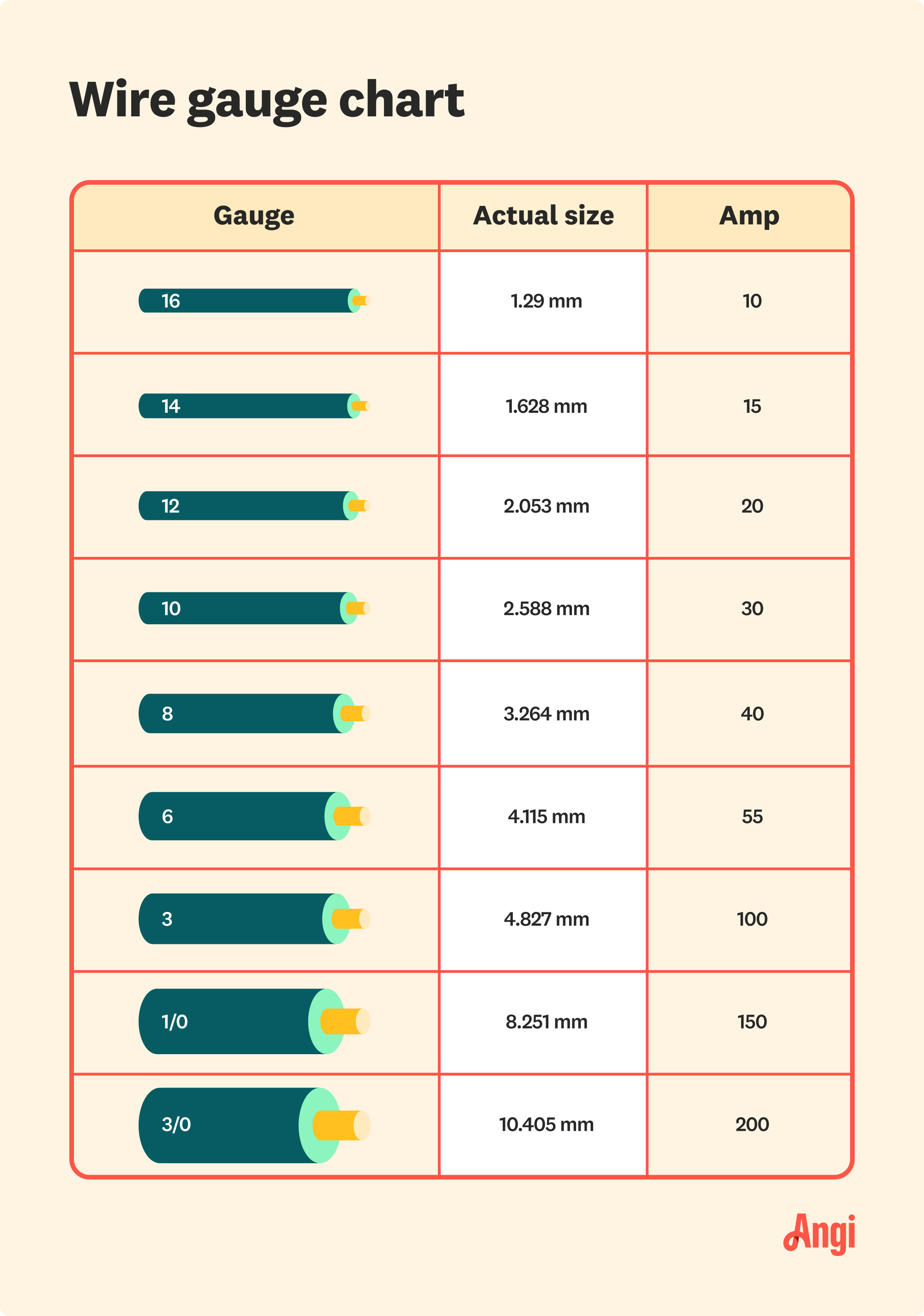
What Is the Correct Wire Size for 100Amp Service? Angi